
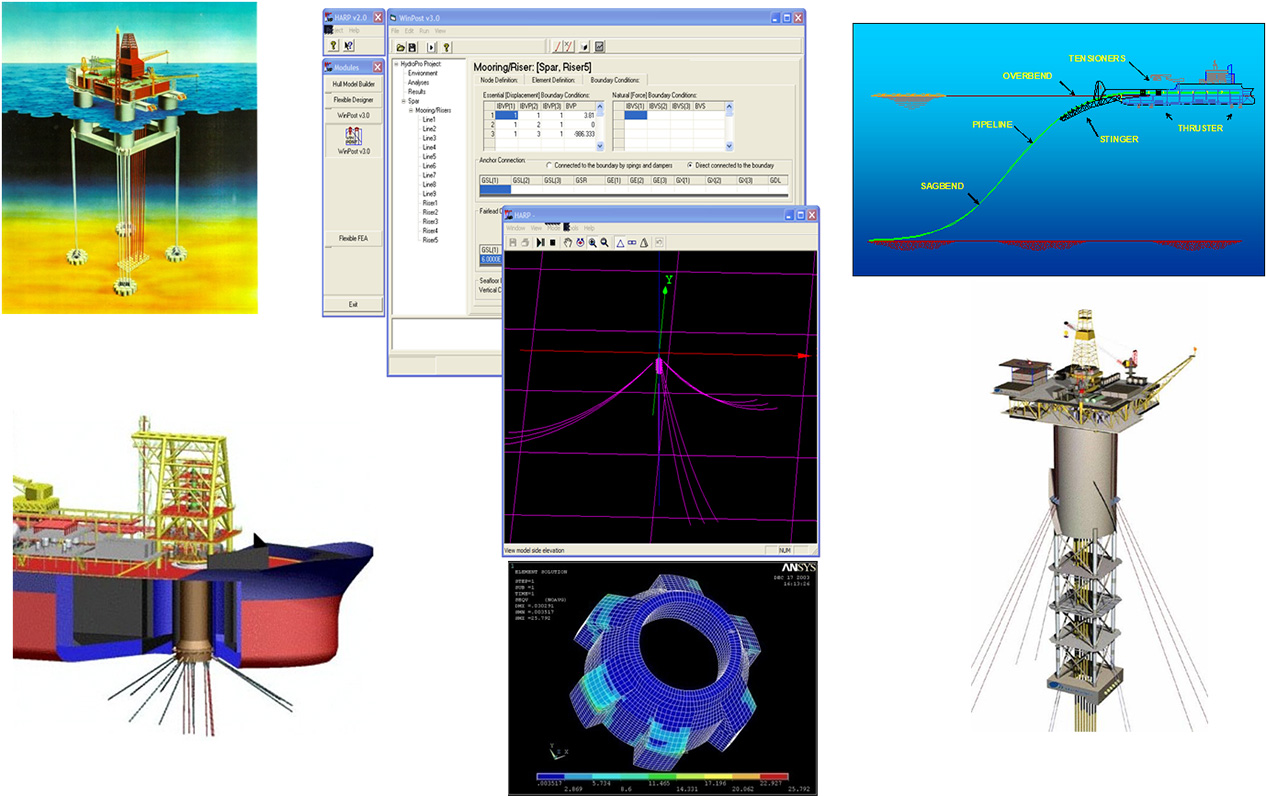
A numerical example of a large diameter 20-in export riser is presented to demonstrate some of the challenging design issues in 750 ft. The programs Shear7 and RISVIC are used to simulate VIV in the frequency and 3D time domain respectively. The riser pipe may exhibit VIV motions for both: in-line and cross-flow current directions. The riser and bottom spool are modeled as a continuous multi-span beam using Flexcom3D and Orcaflex. The main conclusion of this study is that VIV and specifically in-line VIV cannot be ignored because usually becomes one the governing design parameters for this type of applications. Both cases consist of large diameter pipes hanging-off from a collar restrained laterally by guides.

This is a review study of the subject matter, but the main difference is that it considers the spool, bottom bend span and the upper riser as one single structure thus the vibration and soil stiffness interaction of the bottom spool is accounted for in the VIV response of the upper riser spans and viceversa, the vibration response of the riser is accounted for in the bottom spool.įuture bypass and pre-commissioning capabilities for large diameter subsea tie-back spools of incoming import risers that connect to a dual subsea isolation valve assembly as well as pulltubes of deepwater Spars will benefit from the findings of using this approach.

Vortex-shedding design of subsea pipeline spans, and subsea spool tie-backs have been studied by other authors. VIV is often one of the controlling parameter that governs the design of the bottom spool and the riser. The incoming riser is attached to the structure of the receiving platform via clamps that allow no restriction in motion along the axial direction of the riser. The exported fluids are transported by a pipeline from a deepwater Floating Production Installation (FPI) to a valve assembly on the seabed, and then through a tie-back bottom spool to a fixed platform in shallow water. The specific application is for a subsea tie-back, which are common in deepwater field developments. See also the STA CHAINLENGTH Catenary Calculator.This study presents a review and new approach to VIV design of large diameter pipes hanging off from a collar and restrained laterally by guides. STA possesses the experience, knowledge, and resources your organization needs for success.
Orcaflex viv software#
Stewart Technology Associates has yielded impressive results in this area with its clients, and this is due not only to decades of experience, skill, and dedication, but also to the fact that we utilize only the most robust software in Orcaflex by Orcina. Another example cable dynamics example can be seen at CRANE BOOM RECOIL.
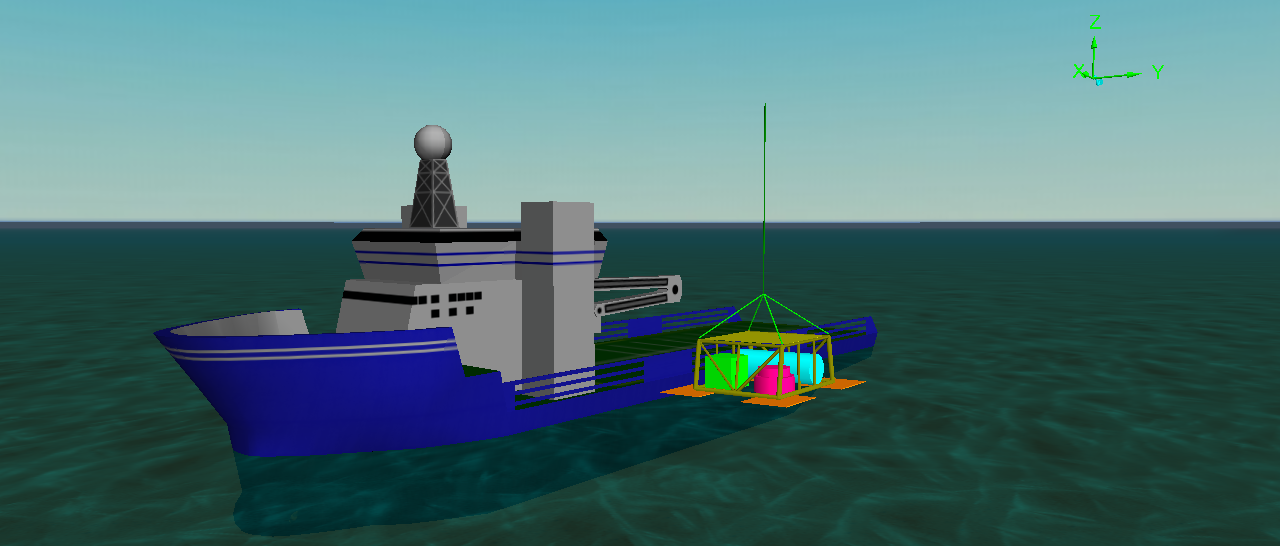
High quality marine and offshore technology consultancy can be expected when working with STA, and this is especially the case when it comes to cable dynamics. With steel (mass density of slings = 40.39 kg/m) the cable dynamics is small amplitude and no galloping occurs. A comparison can quickly be made with steel cables, as they have the same geometry and approximately the same elastic axial stiffness (AE value) but seven times greater mass density. The diagram indicates that cable dynamics are likely to be significant. Note the sling mass density, m = 5.77 kg/m. Key inputs and initial VIV calculations are shown in the table above. Using analysis methods laid out in FHWA-RD-05-083, 2007, for cable-stayed bridges, an Excel tool for calculating the VIV and Galloping of Dry Inclined Cables was developed by Bil Stewart.
